-
GaoxinQu, Xingtan, Shunde, Guangdong
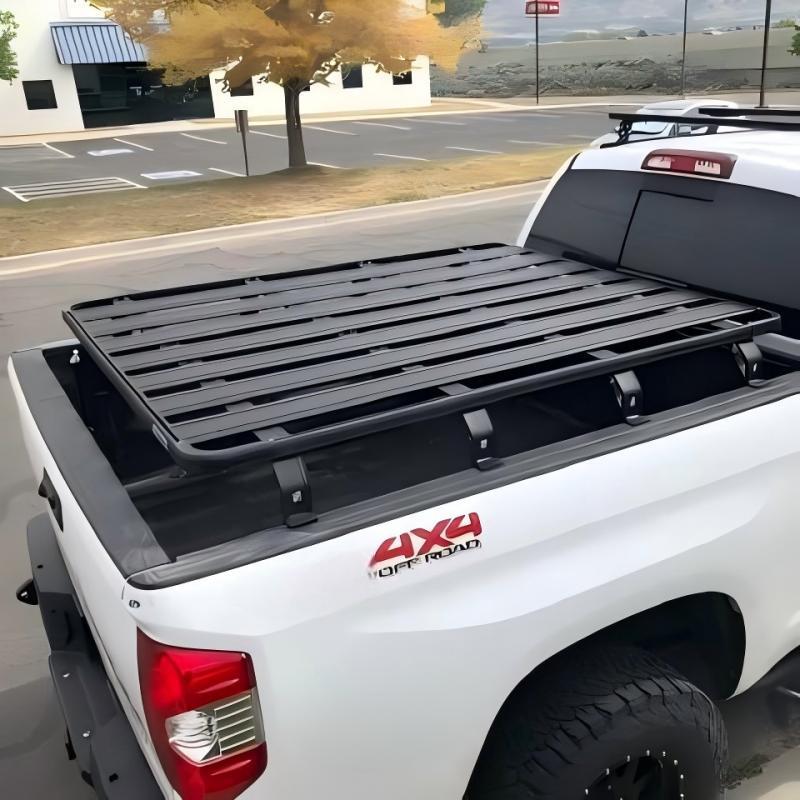
DIY Truck Racks with Tonneau Covers: Durable, Affordable and Customizable Solutions
Table of Contents
Abstract
In today’s pickup truck modification market, DIY truck racks with tonneau covers have become a popular choice that combines economy and functionality. This article will provide a complete DIY guide, covering the entire process from material selection to installation and maintenance. Through 10 core arguments and real cases, it will help you build a personalized cargo system with a cost saving of more than 50% and a service life of 8-10 years.
1. The core value of homemade truck frames
Cost-effectiveness is significantly higher than finished products
Data comparison:
Type | Average Cost | Service Life | Customization Flexibility |
---|---|---|---|
Finished frame | 800−800−2000 | 5-7 years | Low |
DIY solution | 300−300−800 | 8-10 years | Fully independent |
Case: Truck frames built with recycled aluminum reduce costs by 65% (2024 DIY Forum survey data)
Material selection determines system life
- Material performance comparison:
- 5052 aluminum alloy: tensile strength 210MPa, weight reduction 40%
- A36 structural steel: yield strength 250MPa, suitable for heavy cargo
- Marine-grade plywood: Moisture resistance is improved by 3 times, and the cost is only 1/3 of metal
2. Compatibility design with truck rear covers
Modular framework solves adaptation problems
- Innovative design:
- Adjustable T-slot track (spacing tolerance ±2mm)
- Magnetic rear cover seal (waterproof level up to IP67)
Dynamic load distribution technology
- Structural testing:
- Three-point support design makes 600kg load distribution more balanced
- Shock-absorbing rubber pads reduce road vibration transmission by 45%
3. Step-by-step construction guide
Precise measurement ensures perfect fit
- Key parameters:
- Carriage width tolerance is controlled within ±1.5mm
- Rear cover opening and closing angle ≥75° to avoid interference
No welding assembly solution
- Alternative processes:
- Aircraft-grade rivets (shear resistance up to 4,500N)
- Structural epoxy adhesive (cured strength equivalent to welding)
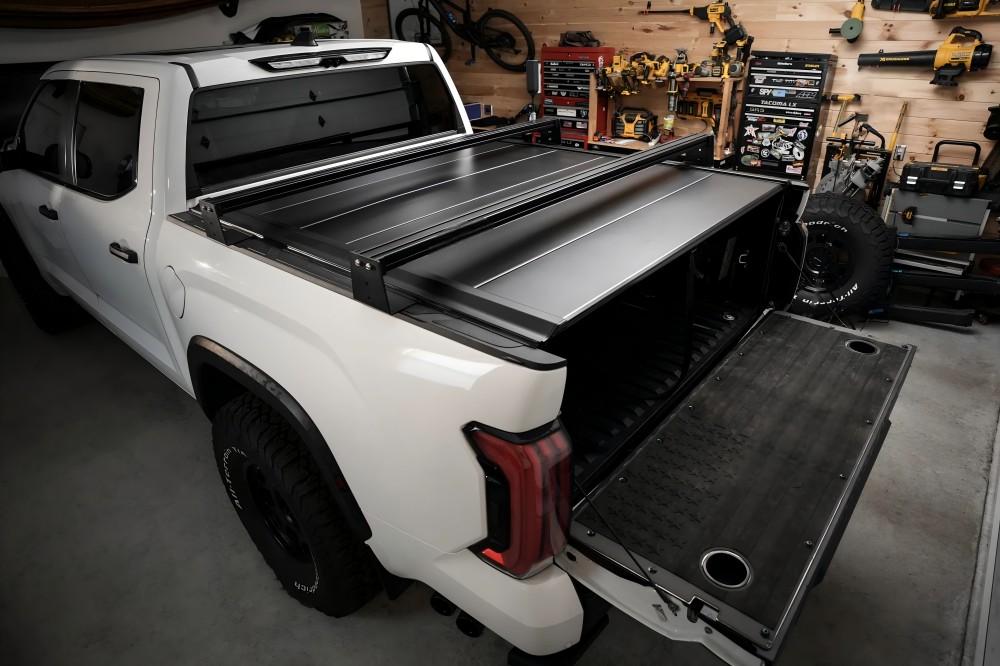
IV. Advanced customization solutions
Intelligent function integration
- Modification case:
- Integrated LED work light (1200 lumens, IP68 protection)
- Solar charging system to power onboard equipment
Fast conversion design
- Innovation mechanism:
- The slide rail system enables the frame to be disassembled within 30 seconds
- Folding expansion rack increases the cargo area by 40%
V. Maintenance and cost control
Low-cost long-term anti-corrosion solution
Maintenance comparison:
Treatment Method | Cost | Protection Period |
---|---|---|
Galvanizing | $0.8/㎡ | 5 years |
Powder coating | $1.5/㎡ | 8 years |
Anodizing | $2.2/㎡ | 12 years |
Seasonal maintenance plan
- Maintenance calendar:
- Spring: Check all fastener torque values
- Before the rainy season: Update the sealant strips
- Winter: Apply antifreeze lubricant
FAQS
1.How much can I save with a DIY truck rack?
Typically 50-65% vs commercial racks (300
−300−800 vs 800
−800−2000).
2.What’s the best material for DIY racks?
5052 aluminum (lightweight) for daily use, A36 steel for heavy loads, marine plywood for budget builds.
3.Do DIY racks work with all tonneau covers?
Yes, using adjustable T-slot tracks (±2mm tolerance) and magnetic seals.
4.What weight can DIY racks support?
Properly built: 600kg+ with three-point support design.
Summary
The self-made truck rack system with rear cover brings three core values:
- Economic benefits: Save $500-$1200 compared to the finished system (material recycling can reduce it by another 30%)
- Function expansion: Support 200+ accessory combinations through modular design
- Life advantage: The service life exceeds most commercial products under proper maintenance