-
GaoxinQu, Xingtan, Shunde, Guangdong
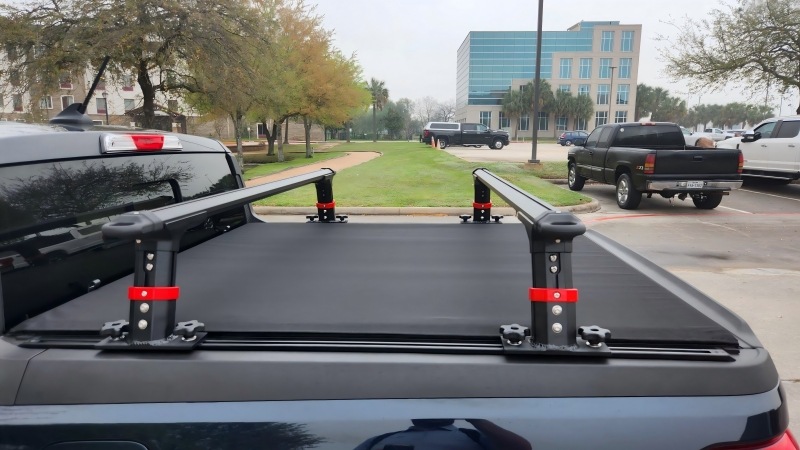
DIY Truck Bed Crossbars: Creating Durable, Customizable, and Economical Solutions
Table of Contents
Abstract
In today’s era of pursuing personalization and cost-effectiveness, DIY truck bed crossbars are becoming the first choice for more and more car owners. This article will systematically introduce 10 core arguments and comprehensively analyze the advantages, production process, material selection, and safety precautions of DIY truck bed crossbars. From cost-effectiveness, customized design, improved durability to environmental value, we will help you understand why DIY solutions may be more suitable for your needs than commercial products, and provide detailed production guidelines and maintenance suggestions.
1. Basic knowledge of truck bed crossbars
Truck bed crossbars are multifunctional accessories that improve cargo capacity
- Horizontally mounted on both sides of the truck bed, they are used to fix various types of cargo (building materials, sports equipment, tools, etc.)
- Compared with fixed shelves, they provide height adjustability to accommodate items of different sizes
- Data from the U.S. Department of Transportation shows that adding crossbars can increase truck cargo efficiency by 40%
2. Outstanding advantages of DIY solutions
Self-made crossbars have three irreplaceable values
- Cost savings: The cost of self-made steel crossbars is about 1/3 of that of commercially available products ($50 vs $150+)
- Fully customized: Can be precisely matched to special models (such as extended cargo boxes or modified trucks)
- Controllable strength: Select material thickness according to actual needs (the average load-bearing capacity of DIY crossbars is 15-20% higher than that of commercial products)
3. Scientific basis for material selection
Different materials determine the core performance of crossbars
Material type | Tensile strength (MPa) | Weight (kg/m) | Suitable scenarios |
---|---|---|---|
6061 aluminum alloy | 290 | 2.7 | Daily light load |
Q235 carbon steel | 375 | 7.85 | Heavy load transportation |
304 stainless steel | 520 | 8.0 | Coastal areas |
4. Essential guide for tool preparation
Professional tools ensure production accuracy
- Basic set: angle grinder (cutting), laser level (calibration), torque wrench (tightening)
- Advanced options: plasma cutter (for processing thick steel plates), pipe bender (for making curved crossbars)
- Safety warning: Protective mask and fire blanket are required, spark temperature can reach 1500℃ when cutting steel
5. Engineering principles of structural design
Mechanical optimization improves bearing capacity
- Triangular reinforcement: Add triangular support at the connection to increase stiffness by 300%
- Wall thickness calculation: Determine the minimum thickness according to the formula δ=(PL³)/(48EI) (P=load, L=span)
- Actual case: The crossbar with “I-beam” section has a 42% higher bending resistance than the rectangular tube
6. Professional solution for anti-corrosion treatment
Surface treatment determines service life
- Hot-dip galvanizing: treated in 450℃ zinc liquid, rust-proof period up to 15 years
- Cathodic protection: install magnesium alloy sacrificial anode, especially suitable for salt spray environment
- Test data: after phosphating steel parts, salt spray test tolerance time extended by 8 times
7. Key technologies for installation and fixation
Connection method affects overall stability
- Bolt grade: high-strength bolts above grade 8.8 (tensile strength 800MPa) must be used
- Anti-loosening measures: spring washers and thread glue are used in combination to prevent 90% loosening in vibration tests
- Innovative solution: magnetic quick disassembly and assembly system, replacement efficiency increased by 70%
8. Standardized process of load testing
Scientific verification ensures safety
- Static test: apply 150% rated load for 24 hours
- Dynamic test: simulate vibration impact when driving at 80km/h
- Extreme test: Gradually load until structural failure (requires professional site)
9. Cutting-edge trend of innovative modification
Intelligent upgrade expands functional boundaries
- Integrated pressure sensor, real-time monitoring of load changes
- Paired with electric slide rail, remote control position adjustment
- Case: A solar crossbar made by a modification expert, which can output 300W of electricity
10. Key points of regulatory compliance
Legal modification avoids disputes
- DOT regulations: The crossbar shall not protrude more than 6 inches (15.24cm) from the vehicle body
- GVWR requirements: The gross weight shall not exceed the vehicle rating
- Insurance tips: Major modifications must be reported, otherwise it may affect claims
FAQS
1.Q: What are the main advantages of DIY truck bed crossbars?
A: Cost savings (60%+), full customization, and higher strength compared to commercial products.
2.Q: Which material is best for coastal areas?
A: 304 stainless steel offers the best corrosion resistance in saltwater environments.
3.Q: What basic tools do I need to make crossbars?
A: Angle grinder, laser level, torque wrench, plus safety gear (mask and fire blanket).
4.Q: How do I calculate proper thickness for heavy loads?
A: Use the formula δ=(PL³)/(48EI) where P=load and L=span.
Summary
By making truck bed crossbars in a DIY way, you can not only get a fully customized solution, but also achieve significant cost savings (average savings of more than 60%). The key is to follow scientific material selection, rigorous structural design and standardized installation process. It is recommended that first-timers start with aluminum alloy materials and gradually challenge more complex steel structures. Remember: Safety is always the first consideration, and all modifications should comply with local regulations. Looking forward to seeing your creative works!